So why is hold attachment such a tricky subject? Most of this comes down to the sheer amount of different holds that are now available, with everything from screw-on holds the size of a penny, to gigantic macros that require multiple people to attach, the route setters choice of holds has grown exponentially over the last few years. Although this has been amazing for route setters, it does create its own set of challenges, with each different hold coming as a new shape, different material and with different options for attachment. The modern day route setter is left with many choices per day as to how they want to attach the holds they use.
Even the choices that seem simple can have hidden complexities. Take bolt-on holds for example. It’s clear that a hold with only a large central bolt hole can be attached with a bolt, but even then there is the choice as to how to pin the hold or even if to pin the hold at all.
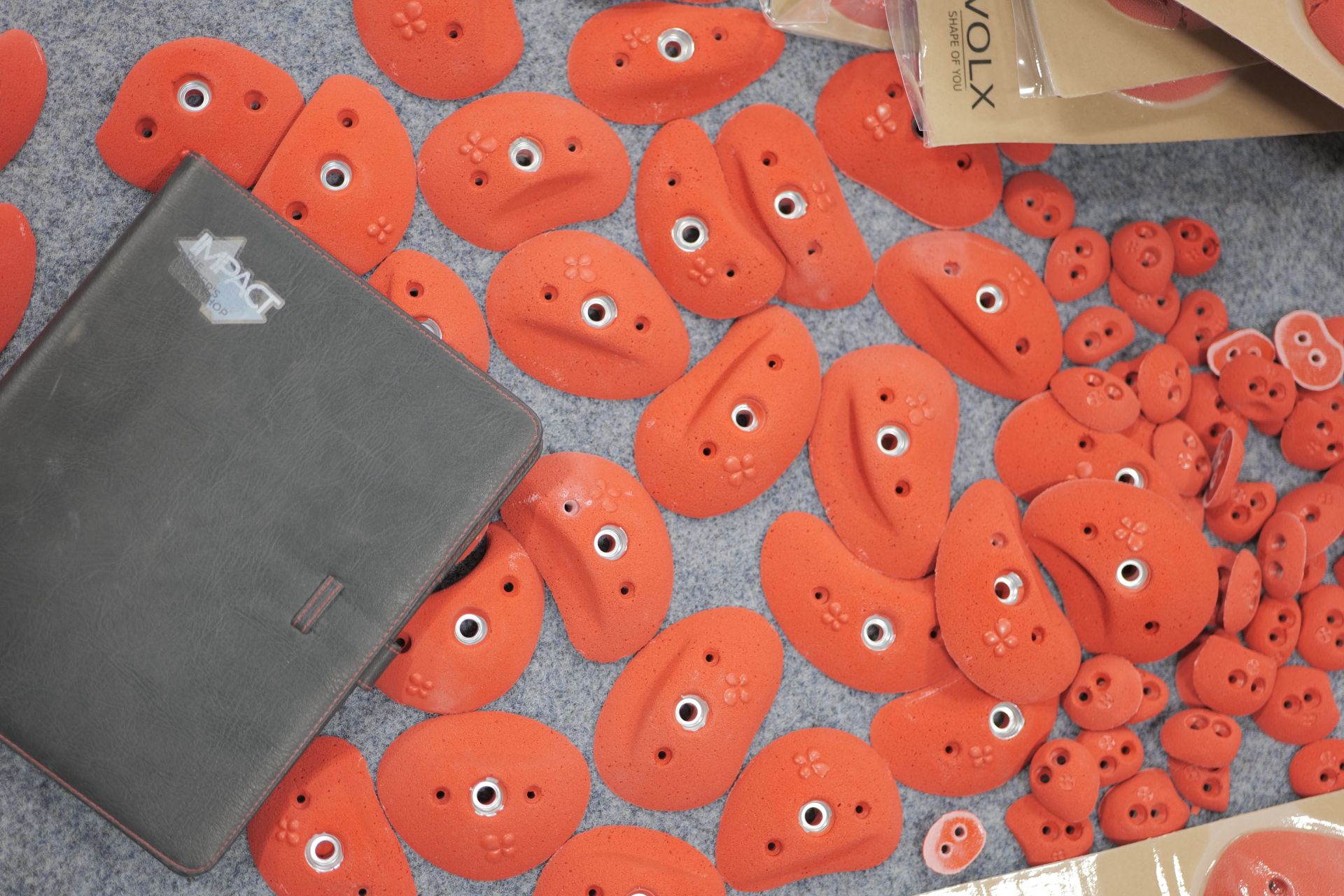
Screw-on holds may also seem simple, as there’s no option other than to attach the hold with screws, but how many screws must we use? Does every screw hole need a screw? What about if one of the 18 screw holes provided ends up hitting a t-nut and can’t be used? Then there’s the real grey area of dual-fixing holds, where the route setter has the choice as to whether they want to screw the hold on or bolt it on. How to determine when a hold is designed as a dual fixing hold or a bolt-on hold with screw holes for pinning is anyones guess and is currently left up to the setter on a case by case basis.
Without clear guidance as to the expected industry standards, route setters are left making hundreds of decisions a day as to whether their chosen method of hold attachment is appropriate. Up until now we’ve relied on the experience of route setters to make sensible and well advised decisions, but as the route setting industry continues to professionalise, there becomes a point where some clear guidance of the expected industry standards becomes necessary.
Currently, each wall has their own policies on the way that they expect holds to be attached in their facility. In the more diligent walls these policies are recorded and shared with each route setter to ensure that everybody is working to the same standards, while in others it’s a more casual affair, based on trust that the route setters judgement is sound and based on the necessary knowledge base. These policies can vary wildly between walls. Here’s some examples of how far away from each other different walls policies can be, based on what we’ve seen at walls across the UK:
Pinning
Policy 1) Total avoidance of pinning holds to protect the wall panels from damage. This includes avoiding pinning holds that have been designed with a pinning hole for a screw to be added.
Policy 2) Pinning every hold in the wall, regardless of size.
Screw-ons
Policy 1)Number of screws to be used left to setters discretion. Holds can be left with attachment points unused if the setters deem it is safe.
Policy 2) Every attachment point must be used no matter the size of the hold.
Adapting Holds
Policy 1)Holds can be ‘drilled out’ (a screw hole added) at setters discretion.
Policy 2) Holds can never be adapted under any circumstance.
Washers
Policy 1)A washer or ‘Lonestar’ can be used with a screw to replace a bolt in any hold.
Policy 2) Washers are never to replace bolts and should only be used to reduce flex or add an extra attachment point as back up.
It’s pretty clear that policies vary pretty wildly across walls in the UK, but what do the hold companies recommend? After all, it’s their products that we’re trying to attach. Let’s take a look at some examples.
Let’s start with the technical data page from one of the worlds largest and most respected hold brands, Cheeta. Here’s the entirety of the section named ‘Fixation and handling of the Holds’.
‘To guarantee optimal safety the user must use all available fixation points. For products that do not dispose of a central bolt, use all screw on points.’
That’s it. That’s the whole section. Delving a little deeper into their catalogue and we can tease out a little more info. The ‘Fixation’ section from the catalogue reads as follows.
‘We paid special attention to the screw holes so that they don’t modify the type of grip of a hold, and cannot be used by hands or feet. Most of the Cheeta holds carry a double fixation system called Dual-fixing. Primary fixation: cylindrical head screws or countersunk screws Secondary fixation: self-drilling wood screws Some of our large holds (especially the flat ones) are delivered with a cork to cover the hole and prevent using it as a mono-fin-ger.’
So here we get a little more info, but it’s maybe not quite as clear as it seems. We can take from the first section that we should use all fixation points, but in the catalogue description it seems to suggest we have a choice of two methods, suggesting we don’t have to use all fixation points and in fact can choose one or another. Scroll through the catalogue and it becomes clear pretty quickly that whilst many holds have this dual-fixing option, they fall right beside many holds which are likely designed as solely bolt-on or solely screw on holds, often with all three types falling into single families of holds with no obvious explanation or differentiation between them.
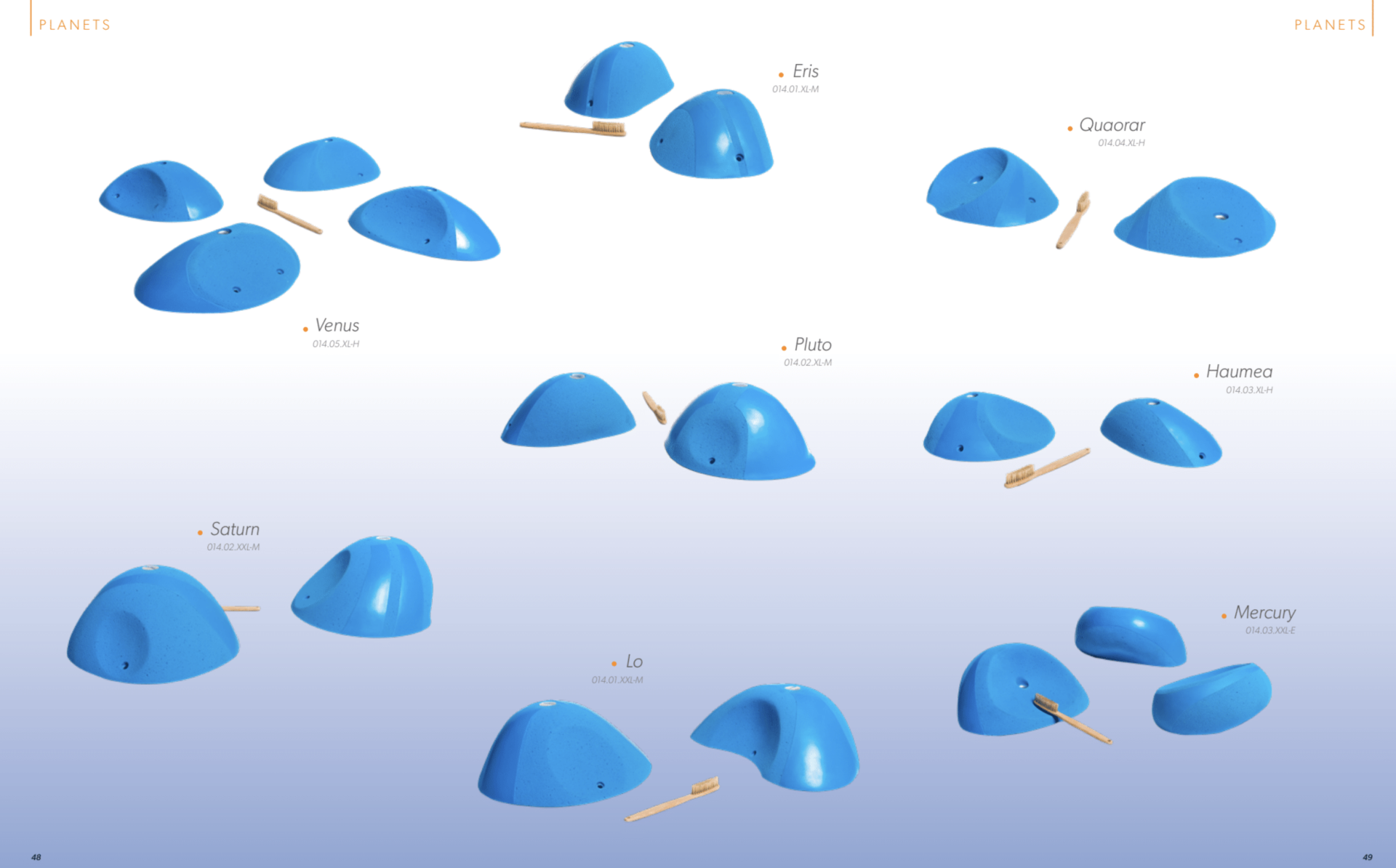
An example page from the catalogue with some holds designed as dual-fixing and others designed as bolt-on holds with pinning holes. All within the 'planets' family and no info to show which is which.
Blue Pill provide much more detailed instruction on proper hold attachment, with recommended torque ratings, screw specifications and reasonable use cases, but still gloss over the harder questions of which of the holds they sell can be screwed on and which are solely bolt-on holds with pinning holes.
Taking a look at Kilter, the many-time winner of the Climbing Business Journal hold company of the year and probably the biggest US hold company, we don’t get many answers at all. Hidden in a maze of disclaimers and T&C’s there is little in the way of information. Look through their selection of holds and it doesn’t take long to get to a set where some guidance would be useful, with single sets that seem to include bolt-on only holds and dual fixing holds in a single bundle.
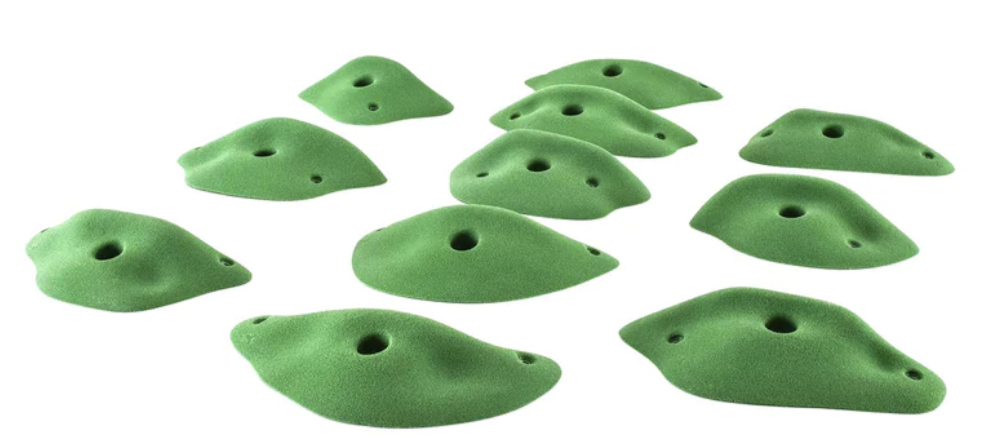
This set for example (NOAH MEDIUM 1 - INCUT EDGES - KX052) would be incredibly useful to have some more guidance for hold attachment. With some holds clearly designed as bolt-on only (a bolt hole and a single screw for pinning) and others that could be designed to be bolted on or screwed on, but no guidance as to which options are recommended or tested.
I could go on all day, but that seems possibly futile. The theme when doing this research was general vagueness and lack of detail in any recommendations I could find, leaving the route setter with the task of deciphering the intention of the manufacturer. Whether this should be done with Poirot style detective work or Derren Brown style mind reading also wasn’t mentioned anywhere I could find, so the decision on that one is likely up to the route setter too.
The one place where I did find some very detailed info was with Core climbing, the biggest UK made hold brand. Their technical info page lays out clearly and unambiguously which hold sets can be fixed in each way and provides a super useful reference for any unsure route setter to find some actual answers. Maybe this is just a symptom of the UK and our legal system (or that we just like things spoon fed to us) but it doesn’t seem like too much of a stretch to ask for something similar from each hold brand.
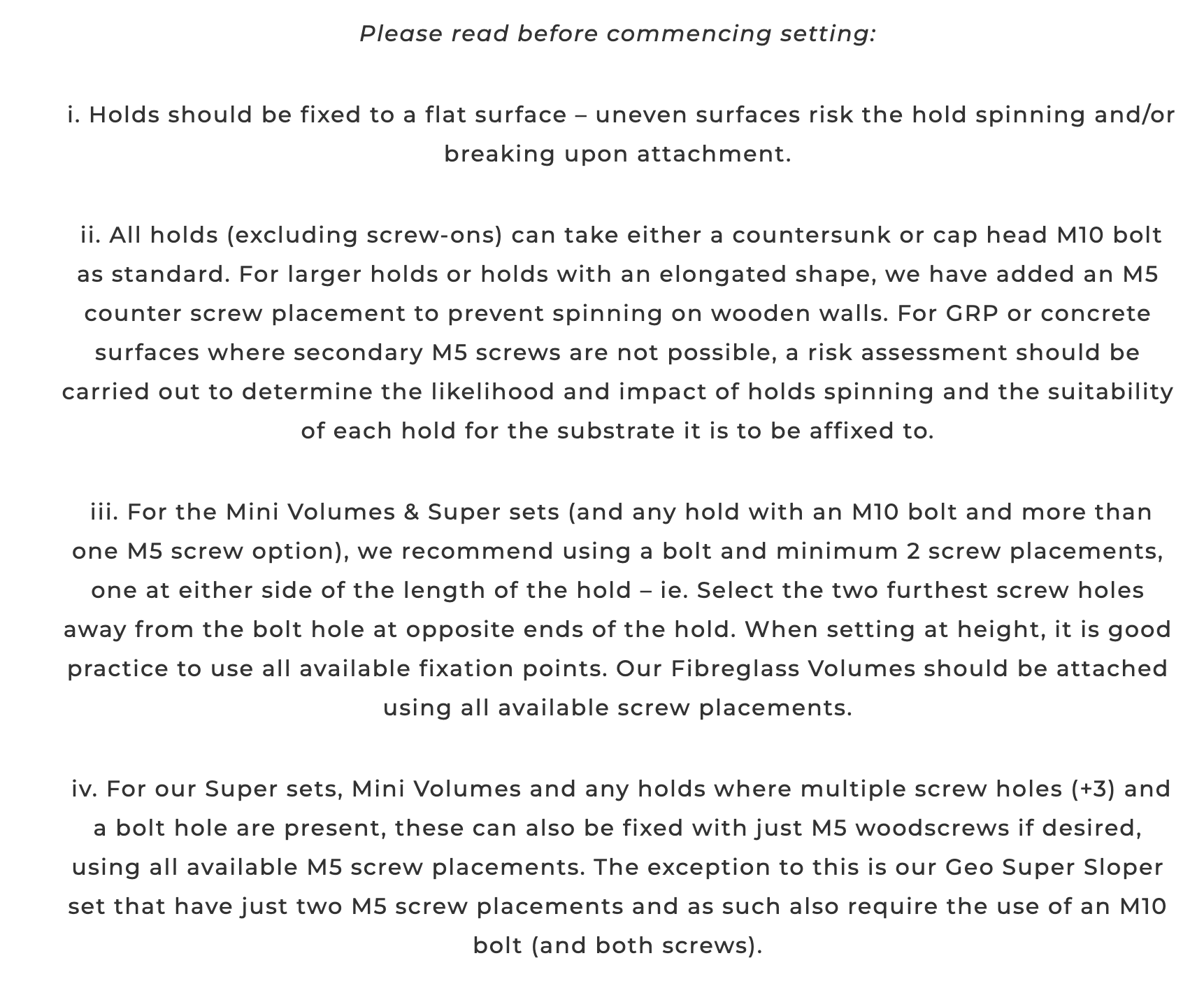
A snippet of Core's guidance. Simple and clear, but giving setters clear guidance as to how each and every hold Core make can be attached.
It seems like now is as good a time as any to also dive into some fringe cases of route setters smashing down the barriers and breaking into hyper-experimentation mode. This trend (no doubt fuelled by the hyper popular @failsetting instagram page) seems to be developing into a one-upping competition of route setters trying to outdo each other with more and more outlandish creations, with hold kebabs, inverted volumes and pretty much anything else wild you can think of being displayed and shared regularly. The issues begin when deciphering which are genuine creations that the public are allowed to climb and which are short-lived jokes, quickly deconstructed after a photo for Insta and before your boss gets back from his lunch break. It goes without saying that almost all of these cases go against the recommended use of the holds or volumes (if you’re lucky enough to find some guidance for the holds you own) and puts the route setter firmly in the firing line (both literally and metaphorically) when sh*t hits the fan.
Write your awesome label here.
Write your awesome label here.
Write your awesome label here.
Write your awesome label here.
All courtesy of @failsetting on Instagram. I've been assured that some of the examples here that I assumed were a joke, were actually up for the public to climb on!
It seems sensible in all situations (and especially the extreme cases like above) to consider the worst case scenario of what happens if something does go wrong. Let’s say a hold that we, as a route setter, have attached has come off and it’s caused a serious accident. In this case we may be asked to defend our professional behaviour, both by our employer and in court. The best way to do this is with records, showing that you’ve got the necessary policies in place and that you’ve got training logs and records to prove your diligence in following these. Some sort of standard operating procedure will also go a long way here in helping to prove you’ve done everything in your power to avoid something like this happening. If you’ve got all this in place you should be able to sleep easy. You can prove that you’ve acted professionally and done everything you need to do to keep climbers safe. The accident may be due to structural failure or hold failure, either way you’re all good as you’ve done your part.
In scenario two your failsetting masterpiece has caused the issue, ripping off the wall and causing the accident (what a shock!). In this case it’s going to be pretty difficult to defend your actions, having either failed to follow your own policies and procedures and having failed to take on board any manufacturer recommendation for use. Even if you have snuck hold kebabs into your standard operating procedure, it’ll likely be shown to be against standard practice by whichever professional witness is brought in to assess the situation in a court hearing. I’m no lawyer, so I won’t pretend to know the details of what could happen if it’s decided that your actions were negligent, but I’ll stick my neck out and take a guess that it’s not so good.
The main thing to consider here is that we, as route setters, are very much responsible for the safety of climbers that climb on our routes and boulders and ensuring a high level of safety should be number one priority at all times. Climbers shouldn’t have to risk assess the climbs that are presented to them as they quite fairly expect the routes and boulders presented to them in a commercial gym to be safe and to a certain standard. If you own a private facility or you’re just setting for yourself then by all means experiment, but experimenting when it’s the safety of the paying customers that is at risk is both irresponsible and unprofessional and could cause a huge amount of damage to the route setting industry if anything did go wrong.
So how do we tackle this tricky subject at Impact? Well we have a few approaches. First is that we’ve put a lot of time and effort into creating our own standard operating procedures for the walls that we work with that outlines in detail the expected standards of hold attachment. We’ve done everything we can to make this as clear as possible, allowing the route setters that work for us to refer to these standards when making decisions about hold attachment. This means that our own procedures are a lot more detailed than anything that we can find from the hold manufacturers online. For example, here’s the section about pinning bolted-on holds:
3.3 ALL bolt-on holds should be pinned to avoid spinning holds.
3.3.1 If the bolt on hold has an additional screw hole (pinning hole) a single screw in the pinning hole is sufficient to stop the hold spinning.
3.3.1.1 In cases of large or flexible holds where more than one pinning hole is provided, a second screw may be added if the route setter deems that the hold may flex.
3.3.2 If the hold does not have a pinning hole, 2 exterior screws must be added to stop rotation.
3.3.2.1 If available, small ‘pinning screws’ (usually 3.5mm x 20mm silver ktx) should be used for this purpose. If not available, use 5mm x 50mm gold ktx.
3.3.2.2 Exterior screws should be added at 45 degrees (between the wall and the hold) to ensure sharp edges of the screw are hidden as well as possible.
3.3.2.3 Exterior screws should be placed to stop rotation both clockwise and anti-clockwise.
3.3.2.4 Exterior screws should be placed to avoid contact with hands and feet wherever possible. E.g. if it is a foothold to be used from above, both screws should be on the underside of the hold where possible.
We also try to give clear guidance about hold attachment on our courses, both in-person and online. The recommendations we make on our courses are taken from our experience of industry standards, the available information from the relevant standard and technical info and fall in-line with our own standard operating procedures. As should always be the case when it comes to safety, we’re clear that setters should err on the side of caution, especially whilst still learning and gaining the experience required to make clear, professional judgements.
We’ve also implemented a sign off procedure for every route and boulder that is set, with every set being checked for a number of key factors before it is opened to the public, with a secondary check from a trained non-route setting staff member to ensure nothing has been missed. These checks are recorded along with our setting grade sheets, to ensure a record of who set each boulder and who signed off the set. It’s likely also a good idea to keep photographic records of the boulders and routes that have been set to refer back to if any claim does arise.
So what could be done about these issues? There’s a few possible solutions that could help. The first being that each hold manufacturer increases the information they have available about the products they produce and sell. There’s no doubt that this is a huge amount of extra work, especially for those that have thousands of shapes that seem to be randomly spread between screw-on, dual fixing and bolt-on holds, but maybe the requirement to produce such information would encourage some slightly more logical decisions that would allow the whole system to make more sense. For example, why not split up sets clearly into some which are bolt-on only and some which are dual-fixing. This would allow a simple table with hold sets and attachment method to provide all the information route setters need (see example below).
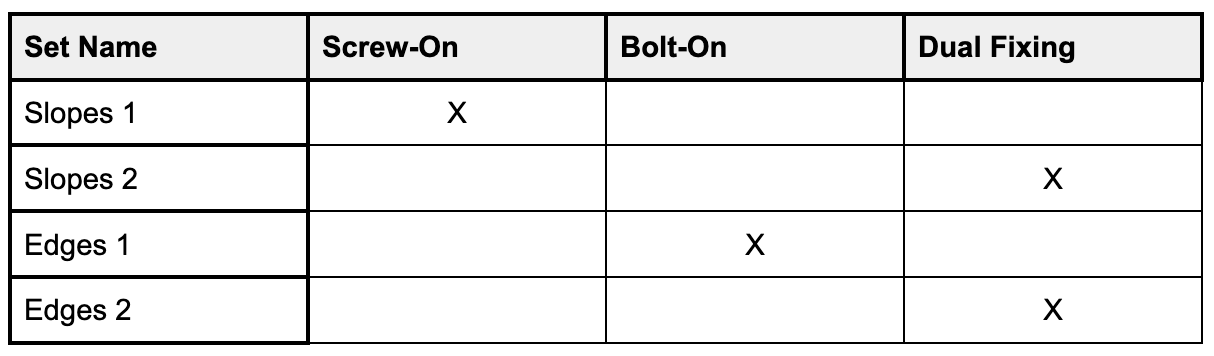
An example table that could be used to easily demonstrate the correct attachment types for each set of holds.
Currently the mismatched sets would cause chaos, with each individual shape having to have its own name and guidance. Maybe something to consider if you’re looking to start a hold brand in the future.
Another solution is that we, as an industry, decide on some universal guidelines that all walls should follow. These can be discussed and decided upon with consultation between hold manufacturers and industry leaders, before being shared with the rest of the industry. This would be an amazing way of standardising practice across a huge number of centres, but as with most things, may be hard to ensure the necessary uptake to feel the real benefits.
In all of this one thing is for sure, that as route setters we need to do our utmost to ensure the safety of the climbers that enjoy our boulders and routes. If we are to keep seeing the industry professionalise and want to experience all of the perks that come with this, we have to act in a professional manner. Creativity is a core tenet of route setting, but our creative ambitions cannot get in the way of our duty of care and our focus should always be on creating and maintaining a safe environment for people to experience climbing.
Need help with your own policies, procedures and documents?